Crew Coordination methods support the improvement across a group or crew of workers. Methods such as visual management or daily huddles allow quick but effective communication that allows a whole team to get on the same page.
Crew Coordination
Method within the Last Planner System that supports collaborative and commitment-based planning and control that
helps develop a reliable workflow.
Daily Huddle
A structured daily check-in for briefly highlight key plans, emerging constraints or safety concerns, changes, and team accomplishments.
Visual Management
A way to manage information visually such that it enables collaboration, open communication, helps track progress and notice disruptions quickly.
Prefabrication
Strategies employed in production to develop assemblies or components off-site to streamline work on-site.
How Crew Coordination Improves Outcomes at KHS&S Contractors
Background
KHS&S Contractors – an international design-assist specialty building company – uses a standard process for coordinating the work across crews. The focus of trade work occurs in weekly cycles, breaking large milestones down to manageable scopes of work to hand out to crews or individual workers. Balancing and leveling this work, along with the necessary equipment, tools, and materials, requires detailed weekly work plans to define all of these activities and match them to the project plan and budget.
Beyond the training and understanding of all elements, KHS&S takes the weekly work plan as a key element for engagement with field personnel. The planning builds from standard Last Planner System (LPS) activities. Still, it is used to align budget information to field activities, plan detailed crew and location assignments, and map work areas and material deliveries.
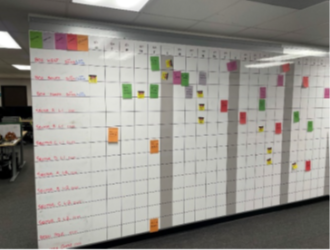
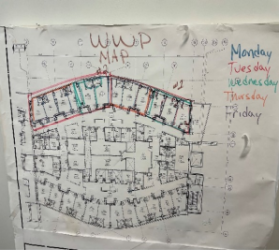
The tasks for each crew member are laid out for the week. This includes the areas of work and day, using color coding as a visual management strategy. The tasks are broken down to match the budget, so the tracked hours are easily linked back to progress, productivity, and billing. Color-coding the daily tasks within the weekly work plan creates a quick visual link between the crew, task, area, and materials across the different visuals used to plan and coordinate work. Each morning, the plan is discussed as part of each crew’s daily huddle.
Daily huddles are conducted each morning before work begins to track the progress and activity of each crew. Using a standard work agenda, the group spends time discussing each crew’s production goal, identifying any current or expected constraints and performing key safety planning for their activities. Before wrapping up, a three minute Lean topic is used each day to maintain the emphasis on continuous improvement. Each meeting also includes a daily stretch and flex and a safety discussion.
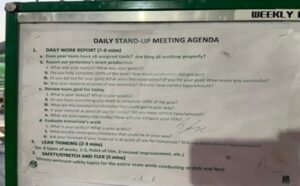
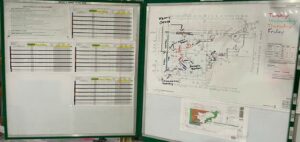
Job boxes are marked and codified with standard tools or equipment to make them easy to find or note if they are missing. Custom safety stickers are created to quickly convey which foreman or craft had completed set training (e.g., Certified to drive a forklift). All serve to shorten the time needed to process the information required for effective planning or communication.
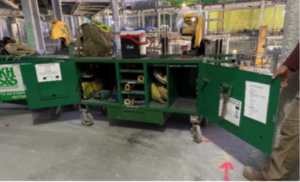
In addition to educating their employees on the 8 wastes in their training curriculum, KHS&S emphasizes enhancing the field personnel’s awareness of waste and how to identify and eliminate it. They leverage visualization techniques to demonstrate these non-value-adding activities on the job site by giving short explanations of waste on stand-up boards, job boxes, and other locations.

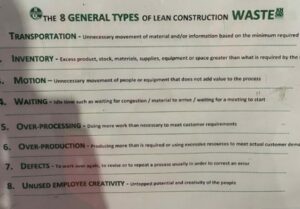
As a result, workers are able to eliminate waste through constant exposure to the concept. They also have daily gemba walks performed by field supervision to focus on eliminating waste and on identifying safety concerns and areas for process improvement.
Conclusion
“Spreading out the Lean principles and initiatives as much as possible throughout their entire organization” is one of the key features of KHS&S’s Lean journey. They employ a thoughtful array of Lean methods, combining them into daily routines and ongoing training.
For example, they have embedded several practical concepts, such as material mapping and color-coded weekly work plans into daily huddle routines to make planning consistent, visual, and easy to understand. This empowers employees to focus on planning and seeing waste in their activities.
In summary, it is apparent that they do not limit Lean methods and concepts to their construction processes; rather, the training and lean concepts are merged with the daily activities and routines to make it part of the culture. In other words, while the pursuit of lean emphasizes the support of field operations and construction tasks for improving production, the processes and culture of lean permeated into the office, departments, and processes at KHS&S.