A3 thinking is a documentation approach for problem solving and reporting on project-related critical decisions using the PDCA method of continuous improvement.
PDCA stands for Plan, Do, Check, Adjust. It is a method for continuous improvement that focus on a cyclic process of planning, execution, monitoring, and learning.
Application
Teams use A3s for problem-solving. This is done by establishing a single 11 x 17-inch sheet of paper to allow the problem solver (author) to fully grasp the issue. The author includes relevant business background information, explores the current situation, and sets goals. By using other sections such as countermeasures, root-cause analysis, and an action plan, the author is able to visualize the whole process, gain alignment with others, and sustain improvement.
A3 Template Structure
Best Practices
- Apply A3 thinking in situations that are hard to define clearly.
- Use this method for chronic or repetitive challenges.
- Use this method for problems that are costly or require significant attention to solve.
- Make information visual.
Process
The A3 process follows the structure of the template to document the problem or opportunity, identify the reasons why it needs to be addressed, and present information to justify the root cause to be fixed (left side).
On the right side of the document, the implementation of the change is captured and tracked to show if the proposed improvement makes an impact, using data to convey the change from the original state.
Do
- Use the PDCA process to ask questions.
- Be patient with yourself and others.
- Start with a pencil and paper or a whiteboard.
- Engage with others.
- Go and observe the current state for yourself.
Don’t
- Fill out a template without following the PDCA process.
- Rush the process or assume that others will be able to follow a template.
- Assume you understand the situation based on secondhand information.
Business Drivers
- Communicate ideas in a simple way.
- Identify and track problems.
- Expose/analyze value to eliminate waste.
- Enhance collaboration.
Benefits
- Creates clear & concise reporting.
- Develops problem solvers.
- Is easy to understand.
- Supports a mindset of continuous improvement.
- Provides information for others with similar problems
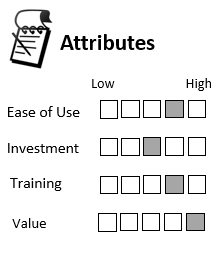
Complementary Methods
- 5 Whys Analysis
- Fishbone Diagram
- PCDA: Plan-Do-Check-Adjust
- DCAP: Detect-Correct-Analyze-Prevent
- Ohno Circle
- Quality Circle
Resources
- Book: Lean Deployment Planning Guide (LCI)
- Book: Transforming Design and Construction – chapter on A3 Thinking
- Lean IPD Blog
- Handbook of Production Improvement Methods