5S is an abbreviation for Sort, Set-in-order, Shine, Standardize, and Sustain (or in the original Japanese – Seiri, Seiso, Seiton, Seiketsu and Shitsuke).
This is a process for waste removal from the workplace through the use of visual controls.
Application
5S is a process that guides people through improving efficiency and making tasks repeatable through defining and organizing the supporting space or resources.
This method emphasizes organizing the workspace in a clean, efficient and safe manner in order to achieve a productive work environment. 5S is used to differentiate required items from undesirable items and to remove unwanted materials and tools that should be stored in an organized fashion.
5S Overview
Best Practices
- Store items based on their function and label them to simplify retrieval.
- Use an organized workspace to reduce waste.
- Place visual signs throughout the work area.
Process
Sort is the first step in 5S implementation. This step emphazises organizing materials and tools so needless items, redundancies, and hazards can be removed from the work area.
Set-in-order is the task of setting out the precise, formal components or tools in the order they are used.
Shine refers to the cleaning and basic maintenance duties workers incorporate into their daily routines.
Standardize focuses on adding formal elements to make the system easy to maintain.
Sustain is the process of continuing and constantly improving upon the system.
Do
- Determine the frequency with which items or equipment are used.
- Implement the tagging technique.
- Store items in the accessible and controllable spots such as toolboxes, Conexus, lay down areas and storage yards.
Don’t
- Neglect to regularly check oil spills, leaks, and equipment damage.
- Forget to meet regularly with workers to review the 5S System.
Business Drivers
- Cost and time savings.
- Increase employee satisfaction and morale.
- Provide discipline and structure for the organization.
- Identify and eliminate waste to generate smooth and efficient flow.
Benefits
- Establish and maintain a clean and productive environment.
- Improve work quality and workplace safety.
- Increase process efficiency.
- Reduce production and set-up times.
- Decrease underutilized floor space.
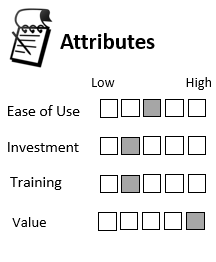